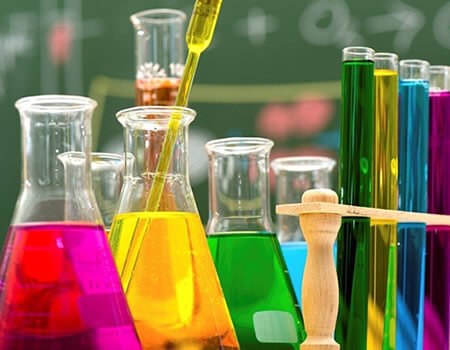
Liquid is a main ingredient in the processing of chemicals, and efficient and effective filtration can improve your bottom line!
From consumable chemicals to industrial chemicals clarity and purity are essential in the pursuit of a high-quality finished product.
We offer a wide variety of Filters for Chemicals Processes
- Conventional Filter Press
- Membrane Filter Press
- Fully Automatic Filter Press etc..
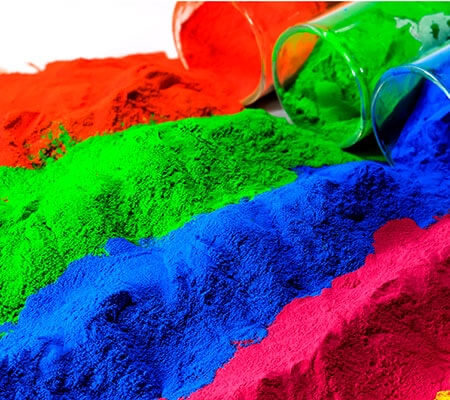
Whether you’re processing raw materials for production of colors, pigments dyes and inks, or refining finished product, our full Line of membrane filter press systems can help.
Our Industrial Membrane Filter Press Filtration Technology Are Used in a Number of Processes, a Few Specific Examples Include
- Art Paste
- Azo Pigments
- Ceramic Pigments
- Chrome Oxide
- Copper Phthalocyanine
- Diazo Dyestuffs
- Dry Pigment Dispersion
- Gamma Acid
- Indianthrene Blue
- Intermediates
- Color-Lacquers, Master Batch Concentrate and Paste
- Pearlized Pigment
- Phosphorescent Blue
- Pigment Flushing
- Printing Inks
- Reflex Blue
- Ruben Red
- Inorganic & Organic Dyestuffs
- Iron Hydroxide
- Iso Gamma Acid
- Lead Chromate
- Magnetic Tapes
- Methyl Violate
- Molybdate Orange
- Monastral Green
- Orazet Yellow
- Paint and Paint Bases
- Paper Coating Colors
- Paranitrotoluene Sulfonic Acid
- Rutile Pigment
- Salt Grinding
- Toner
- Titanium Dioxide
- Wax Crayons
- Zinc Chlormate
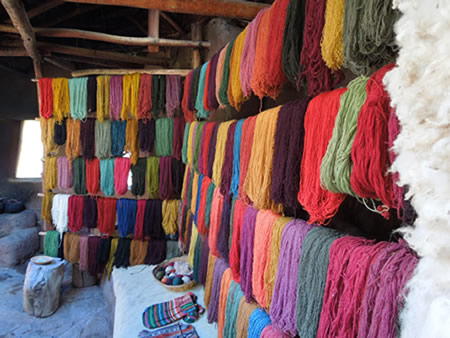
Reactive dye is a class of highly coloured organic substances, primarily used for tinting textiles. Dyes and pigments find use in a variety of applications for textiles, paper, leather, inks, plastics and paints, perfumes & cosmetics, agrochemicals and pharmaceuticals.
Apart from uses in conventional filter press, our new technology membrane filter press are working very nicely.
Key areas we target are de-salting, cake washing for better inorganic removal, black particle removal filters from colours and dyes.
Membrane filter press technology is routinely used by a wide variety of process industries to concentrate, purify and improve final product quality. Its popularity within the dye industry is growing as dye manufacturers discover that this technique is a reliable and cost effective means of improving yield and product quality.
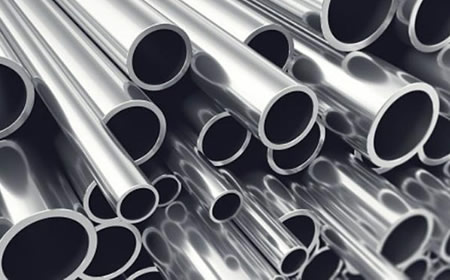
Presently these P.P. Filter presses are also recommended for clarification of solutions as well as waste water effluent treatment & sludge dewatering process in steel industry.
By using the filter press in the above process the total operation of sludge bed drying is eliminated thereby reducing the large space of sludge bed eliminate the problems of overflow of the beds.
With years of practical knowledge since 1972 & after installing more than 4500 standard filter presses & more than 50000 P.P. Plates we have achieved some more practical data in the line of filtration and supplied our many many filtration plants to various steel industries as under .
We have supplied our filter presses in many reputed steel tubes / wire manufacturing industries in india in their E.T.P. / galvanizing (acid pickling neutralization) plant. Some of them are .
Company Name | City Name |
---|---|
Gujarat Steel Tubes | Karigam |
Ambica Tubes | Ahmedabad |
Technocrafts Industry | Mumbai |
Brihan Maharastra Steel Tubes Ltd. | Thane |
Zenith Ltd. | Tarapur |
Ratnamani Metals | Chatral |
S.L.S. Tubes Ltd. | Chatral |
Devine Tubes Ltd. | Chatral |
Asian Tubes Ltd. | Chatral |
Shah Alloys Ltd. | Thor, Kadi |
National Steel & Agro Industries | Indore (M.P.) |
Katariya Wire Industries | Ratlam (M.P.) |
D. P. Wire | Ratlam (M.P.) |
Bhandari Foils & Tubes Limited | Dewas (M.P.) |
Lloyds Metal & Allied Industries | Murbad |
Suraj Stinless Ltd. | Kadi, Gujarat |
Rajratan Gastar Wolf Ltd. | Indore |
Phoenix Foils Pvt. Ltd. | Valsad, Gujarat |
Oswal Industries (Foundry Division) | Kalol, Gujarat |
Welspun Gujarat Stahl Rohren Ltd. | Kutch, Gujarat |
Shubhlaxmi Metals And Tubes P. Ltd. | Umergaon, Gujarat |
Aradhya Steel Wires Pvt. Ltd. | Davangere |
L & T Ltd. | Dhar, (M.P.) |
Amitasha Enterprise | Nagpur |
Star Circlips Ltd. | Nagpur |
Shilpa Re-rolling Pvt. Ltd. | Nagpur |
Eros Metal & Infrastructure | Nagpur |
Unitech Power Transmition | Nagpur. & Many Many More |
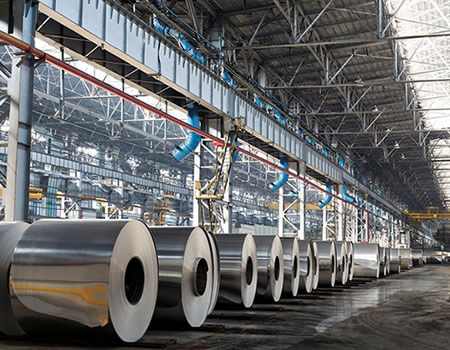
We understand that you are the dealing in rolling or re-rolling manufacturing. We take this opportunity to introduce ourself as a leading manufacturer of various sizes & types of polypropylene filter presses used for many filtration conditions in many varied industries .
Presently these P.P. Filter presses are also recommended for clarification of solutions as well as waste water effluent treatment & sludge dewatering process in rolling mill industries.
By using the filter press in the above process the total operation of sludge bed drying is eliminated thereby reducing the large space of sludge bed eliminate the problems of overflow of the beds.
We are sending herewith our new designed effluent treatment plant plan for your ready reference & knowledge .
Latest & Modified Process of Steel- Rolling Effluent Treatment Plant

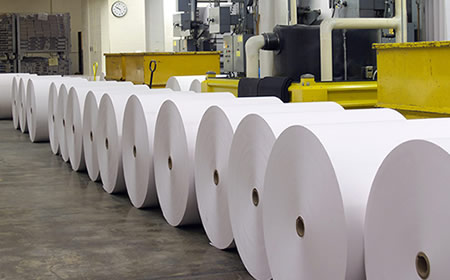
Presently these P.P. Filter presses are also recommended for clarification of solutions as well as waste water effluent treatment & pulp sludge dewatering process in paper industries.
The paper industry uses a lot of water and is more and more restricted by environmental rules and regulations. Besides, the effluent of the paper industry can have distinctive characteristics, like high cod load,high temperature,high calcium carbonate,high suphur,extreme PH and soon.
Yo-tana has developed a filtration de-watering system specifically for the paper industry. This innovative process makes it possible to produce recycled paper with very less discharging effluent. A significant reduction in both energy usage and water consumption is achieved, resulting in considerable savings & ultimately has resulted in the development of this effective water re-circulation and purification process.
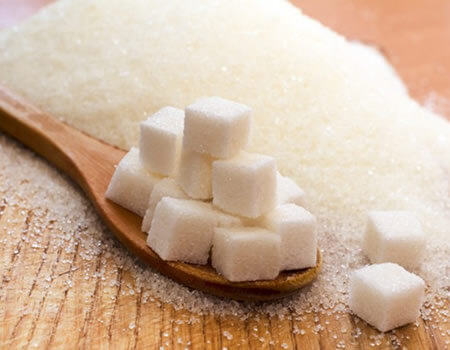
Various methods are available for treatment of sugar mill effluents, some of which may be used in combination. Relatively simple methods, such as the use of settling ponds or lagoons, can be used for preliminary effluent treatments. Although these methods has failed & considered inefficient as it requires the large space of sludge bed, creates the problems of overflow of the beds during monsoon & very laborious to handle the settled sludge..
The extent to which effluents have been treated prior to discharge will have a substantial influence on their polluting potential. As a consequence of the materials and processes undertaken in the sugarcane mill, raw effluents tend to be rich in organic matter, including carbohydrates, and consequently high in COD/BOD which has to be treated and de-watered & makes it in semi-solid form by the way of pressure filtration as per the PCBS pollutant discharge rules.
The best way for de-watering of effluent sludge of sugar mills is filter presses. Yo-tana has developed a special filter presses for the same.
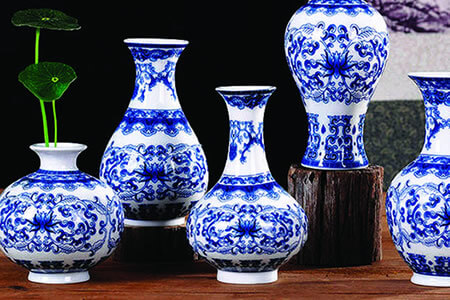
Presently these P.P. Filter presses are also recommended for clarification of solutions as well as waste water effluent treatment & sludge dewatering process in ceramic industries.
The ceramic industry uses a lot of water for shaping machines / chamfering machines and sludge generated therein is more and more restricted by environmental rules and regulations.
Yo-tana has developed a filtration de-watering system specifically for the ceramic industry. This innovative process makes it possible to convert the slurry / sludge into semi-solids cake form with very less moisture content.
By using the filter press in the above process the total operation of sludge bed drying is eliminated thereby reducing the large space of sludge bed eliminate the problems of overflow of the beds and water can be re-circulated / reuse.
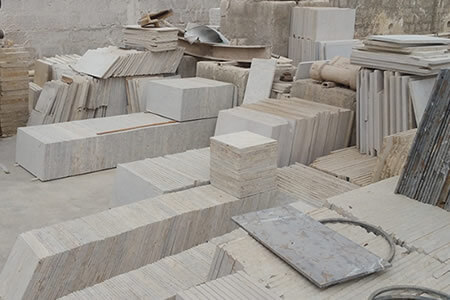
For Marble Waste Sludge De-watering Application
Presently these P.P. Filter presses are also recommended for clarification of solutions as well as waste water effluent treatment & sludge dewatering process in marble processing industries.
By using the filter press in the above process the total operation of slurry disposal through tanker thereby wasting a large amount of water & increasing recurring expense of tanker transportation can be avoided. Apart from this the whole process is environment friendly.
Waste Water Treatment Using a Filter Press in Marble & Stone Industries
Filter press is being used in a very wide application in different process industries as well as in different effluent treatment plant since many years.
Here is a special application of filter press in the waste water treatment for the marble & stone industries.
The waste water treatment plant as whole consists of several equipments like waste water collection tank, static decanter (settling tank), slurry homogenizing & filter press.
Present System
The marble units use one or more gangsaws for cutting the marble stones.
In the process, water is used as coolant to cool the gangsaws cutters.
Normally about 100 m3/hr water per gangway are used. The water coming out from gangsaw is milky in nature & carry about 0.2 % to 0.5 % fine marble powder.
This water is over flown in series of kachha or concrete under ground pits in large area underground tank in the main plant. From here the slurry is pumped up into the decanter (settling tank). on retention of this water for some time, results in the settling of the fine powder in the form of a marble slurry which is discharged in open drains, or taken out in the tankers (it has 80 % water & 20 % solids), stored in open pits for sun drying. Finally marble cake / powder are discharged & or left in & around the area. The supernatant water is mixed with the fresh tube well water and is stored in underground or overhead tanks and is recycled to the gangsaws operations.
By adopting the present system the marble processing units require large land, throw away a large quantity of water in the form of marble slurry (approxi. Upto 40,000 ltrs. / day), frequent repair and maintenance of the pumps besides unclean, dirty & inconvenient environment under which they have to operate. The discharge of marble slurry is difficult and is resulting in a serious effluent and in turn pollution problems.
New Water Filtration System
Based on the detailed studies and r & d carried out by our technical team, a system has been developed, designed, installed, commissioned and successfully operated and reuse 2,500 ltrs. Water per hour (with the pump flow of 7.5 M3 / hour) and automatically de-watered 3400 ltrs. / hr. Marble slurry, discharging a truckable cake @ 2.4 tons / hr. (having 20 % moisture & 80 % solids) and approxi. 40 tons per day of 16 hours working at Arihant tiles & marbles Pvt. Ltd. Udaipur. (rajasthan).
The well developed, new filtration system for marble processing plants, operating one / two / three & more nos. Of gangsaws is provided.
The slurry then pumped to a filtration system fully / semi automatic filter press operating at a high pressure and with a mechanism to de-water the marble slurry to form a hard & semi dry cake and further removing water by employing the compressed air. This results in obtaining more solid truckable marble cake which can be disposed for land filling or reused for manufacturing some marketable products.
The clear water coming out of the filtration system is taken into rcc underground tank or over head mild steel tank. This water is pumped back to the gangsaw operations. Thus, system provides total removal of marble powder in the form of a solid cake and recycling of the clear water. It does not require large volumes of M.S. Tanks and utilize the existing facilities.
It is unique system fir zero pollution and complete reuse of the water for the marble / granite processing units.
Operation of The Filter Press
The tank slurry is transferred to the filter press where the process of dewatering is done. The filter elements used in the filter press are high pressure chamber plates with center feeding. The batch cycle is made shorter and faster by appropriately selecting the number of plates and the flow of the pump. After the filtration is completed using high pressure feeding system, the cake formed in between the plates I.E. The chamber is free from extra water and may contain a minimum of moisture. The filter press is now ready for decaking. The opening mechanism in yo tana filter press is made as such that all the cake from each chamber is dropped down on the conveyor mechanism. The filtration I.E. The clear water coming out during the filtration is the clear water and can be directly sent to the clear water tank & then reuse for gangsaw operations.
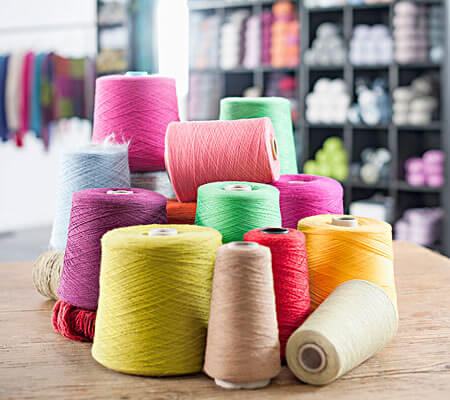
Wastewater from textile industry contains various contaminants such as dyes, surfactants and heavy metals. Textile dyes have synthetic origin and complex aromatic molecular structures that make them difficult to biodegrade when discharged in the ecosystem. The objective of this study was to examine the decolourisation of textile effluents containing cationic dyes by filtration-adsorption on wood sawdust from two different origins; fir as an example of a conifer tree, and beech as an example of a deciduous one, and to explain the adsorption mechanism.
The process of dye removal was applied to a synthetic effluent in batch mode.
By using the filter press in the above process the total operation of sludge bed drying is eliminated thereby reducing the large space of sludge bed eliminate the problems of overflow of the beds.
With years of practical knowledge since 1972 & after installing more than 5000 standard filter presses & more than 50000 P.P. Plates we have achieved some more practical data in the line of filtration and supplied our many many filtration plants to various textile industries as under.
We have supplied our filter presses in many reputed textile industries in india in their E.T.P. Plant. Some of them are.
Company Name | City Name |
---|---|
Modern Terry Towel Ltd. | Sanand, Ahmedabad |
Ashima Syntex Ltd. | Ahmedabad |
Aarvee Denim & Exports | Narol, Ahmedabad |
Chetan Textiles (C/o. Pradeep Overseas) | Changodar,Ahmedabad |
Bharat Vihay Mill | Kalol |
Madura Coats (Vivella) Ltd. | Panoli, Ankleshwar |
Himson Textile Engg. Pvt. Ltd. | Surat |
Varun Dying & Printing Mills | Surat |
S.S.P. Treads | Delhi |
S & P Threads Ltd. | New Delhi |
Rishabh Speciality Yarns | Udaipur |
Rajasthan Textile Mills | Udaipur |
Rajasthan Textile Mills | Bhavanimandi, Rajasthan |
Wellspun Polybuttons Pvt. Ltd. | Gurgaon, Haryana |
Hind Spinners | Rajgarh, Bhopal |
Abhishek Industries Ltd. | Barnala, Panjab |
Sunflag Ltd.. | Tanzania. (Exported) & MANY MORE |
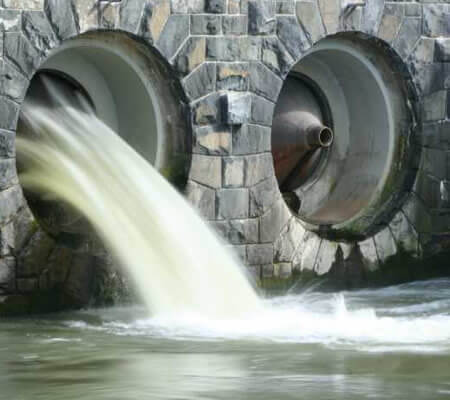
Wastewater Treatment of a Wastewater Plant via Using a Filter Press
On many production processes wastewater accrues which cannot dumped directly in the public sewerage system. In this cases the wastewater have to be treated and the accrued sludge have to be dewatered.
The requisition to the wastewater treatment, the sludge dewatering and finally to the filter press increase with complexity of upstream production processes.
If the waste water accrues in continual constitution and quantity it is relative easy to build an effective wastewater treatment.
But if the wastewater always change their total solid (TS), you need a plant which automatic customize to the changes in waste water. Also the filter press in cooperation with the filter cloth have to cover a wide spectrum of sludge properties.
The foundation pillars of purpose are always the observation of the limit values to water discharging and the competitive disposal of filter cake.
To layout the filter press or if necessary a diaphragm filter press you have to respect raise of the wastewater quantity via expandable filter presses. Thereby it is secured, that the filter press will not be the needle eye of the whole production.
But also in continuous production the requirements on the availability of filter presses and diaphragm presses are high. Nobody can afford a breakdown of the wastewater plant for several days. We can assure highest availability for your plant, because of our high quality standards, best skilled service staff and flexibility.
As you aware, these P.P. Filter presses are widely running for clarification of solutions as well as for dewatering process in starch industries for liquid glucose, maltodextrin, dextrose, sorbitol, corn fiber, gluten etc.
After gathering 35 years of experience in this field since 1972, we have supplied our many filter presses to various starch industries. Some of well-known names as under :
Company Name | City Name |
---|---|
Anil Starch Industries | Ahmedabad |
Maize Products | Ahmedabad |
Gujarat Ambuja Proteins Ltd. | Himmatnagar, Gujarat |
Gulshan Sugars | Jhaghadia, Bharuch, Gujarat |
Kasyap Sweetners | Budnawar, M.P. |
Kasyap Sweetners | Vapi, Gujarat |
Rajaram Maize Products | Rajnandgaon. Chh. |
Rajaram & Brothers | Mandsaur, M.P. |
Tirupati Starch Industries | Indore, M.P. |
Unique Sugars / Universal Starch-Chem | Dondaichcha, M.P. |
Sukhjit Starch & Chemicals | Phagwara, Panjab |
Sukhjit Starch Mills | Nizamabad, |
Sukhjit Starch Industries | Malda, West Bangal |
Santosh Maize & Industries | Salem, Tamil Nadu |
Santosh Starch Products | Bhachau, Gandhidham |
Rai Agro Industries | Sangrur, Panjab |
Bharat Starch Industries | Yamunanagar, Haryana |
Bharat Gluco-Bio | Karnal, Haryana |
Goodrich Carbohydrates | Karnal, Haryana |
Sahyadri Starch Industries | Mumbai |
Mahaan Biosys | Paonta Sahib, H.P |
Pioneer Industries | Pathankot, Panjab |
Honest Derivatives & many more.. | Jalgaon |
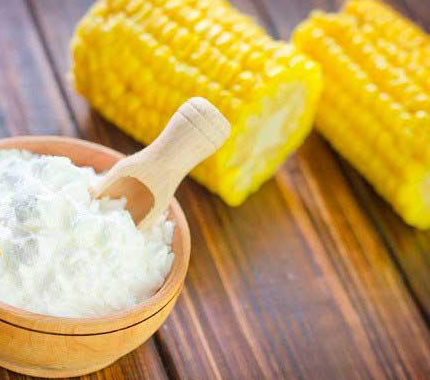
The extraction and processing of starch from agricultural commodities is one of the most important agro industries worldwide. The main raw materials of starch are corn, wheat, potatoes, tapioca and rice. The by-product gluten is almost exclusively used in the food and beverage and animal feed industry.
Starch, however, as well as being mainly used in the food and beverages industry, is also used in its raw or modified form in many applications in industries such as textiles, paper, plywood, adhesives and the manufacture of pharmaceuticals.
Filtration processes have a significant influence on the efficient use of existing production facilities and the quality of the final products. The know-how of yotana competent experts can provide an important contribution to the improvement of your specific filtration process by helping you select an optimal filtration equipment I.E. Filter press.
We are happy to announce that our membrane filter press (mechanical cake squeezing process) which has excellent results for making very less moisture content in the pressed cake. The results achieved in the working of membrane filter presses are :
Gluten | Moisture content in the press cake are around 40 % which is almost 25 -30 % less compared to the moisture in conventional Filter presses. |
L.G. | Moisture content in the press cake are around 33 - 34 % which is almost 25 -30 % less Compared to the moisture in Conventional Filter Presses. |